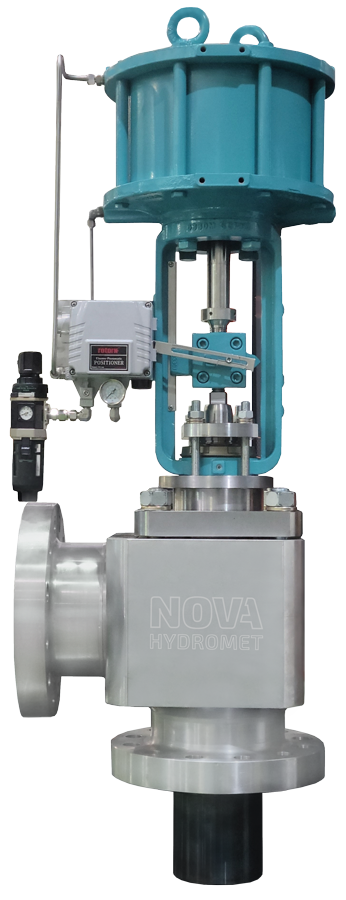
NOVA
Severe Service Control Valves
We take a holistic approach to designing control valves, trim, and blast tubes for Hydromet. These are complex systems with multiple factors impacting valve performance and lifespan.
Downtime related to Hydromet products cost mineral processing facilities hundreds of millions per year. NOVA has the technology, and most importantly, the knowledge to eliminate unpredicted valve failure and maximize your return.
As Letdown Control Valves act as the lynchpin for autoclave circuits, it is critical to use the right materials in their construction. Our designs aren’t pieced together — they are created from mono blocks of materials like Titanium Grade 12.
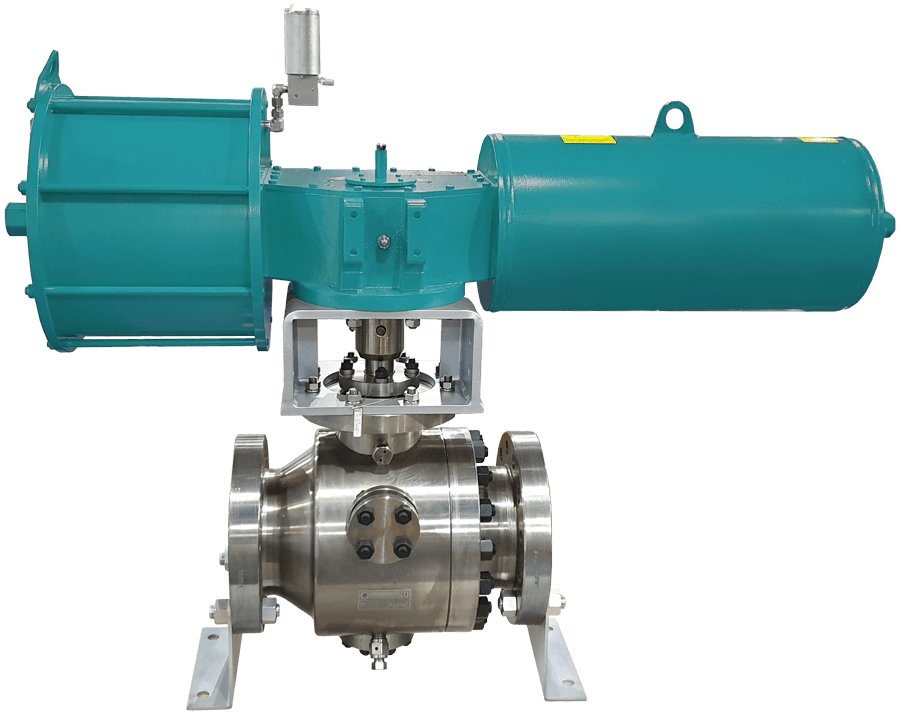
NOVA
Severe Service Ball Valves
NOVA specializes in ball valves with material technology and valve designs that meet the most stringent standards of today’s hydrometallurgy industries.
These high-performance valves are designed and manufactured to solve severe service problems effectively and efficiently.
Tight Quality Control
Engineering
Assembly
Testing
Our vertically integrated manufacturing process allows for exceptional traceability and accountability, resulting in consistently high-quality equipment delivered to your site on time and on budget.
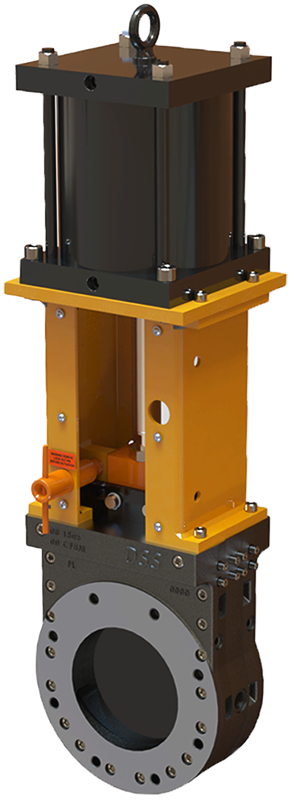
DSS Valves
Severe Service Knife Gate Valves
DSS Valves offer zero leakage, bi-directional isolation that reliably meets or exceeds API, ASME and MSS specifications and can isolate from full vacuum to ASME Class 1500/PN 250 pressures (3750 psig/250 barg).
NOVA has supplied over 10,000 GSGs in leaching circuits around the world on six continents, including most HPAL and POx facilities. DSS manufactures a full range of isolation valves and a unique slurry throttling control valve.
Guided Shear Gate Design (GSG)
The DSS Guided Shear Gate Design (GSG) consists of two key elements: a shearing tip and internal gate guides.
From open to close the gate is guided the entire way, removing any option to deflect when solids are encountered. When the material is struck by the shearing tip, it is fractured and angled away, enabling zero leakage where the gate meets the primary seal.
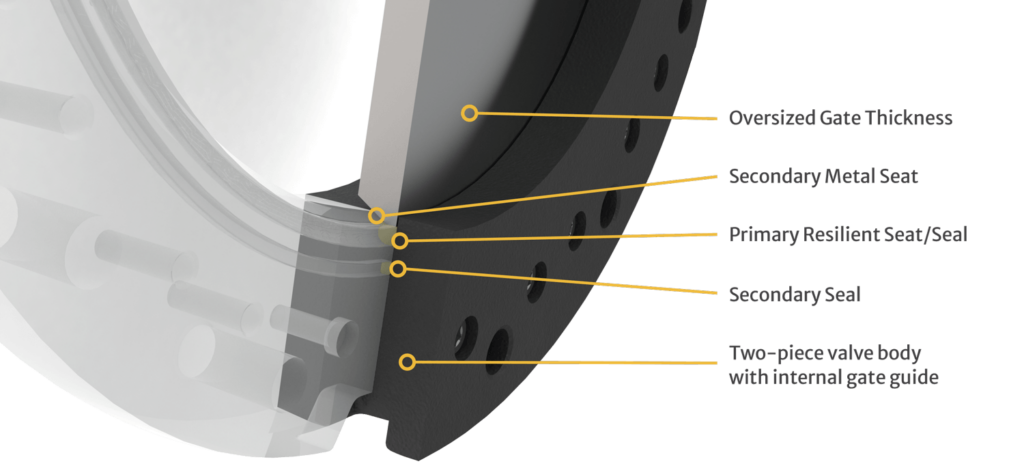
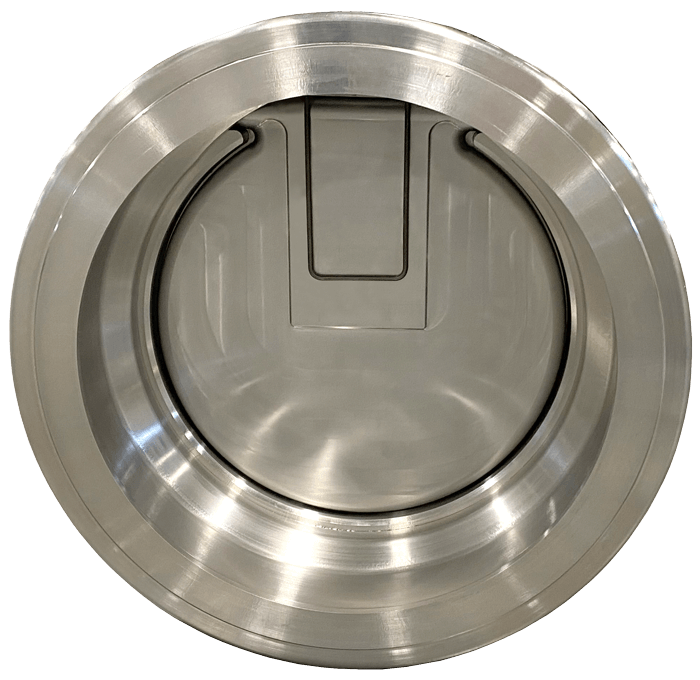